- Home
- browse videos
- What's inside a wind turbine?
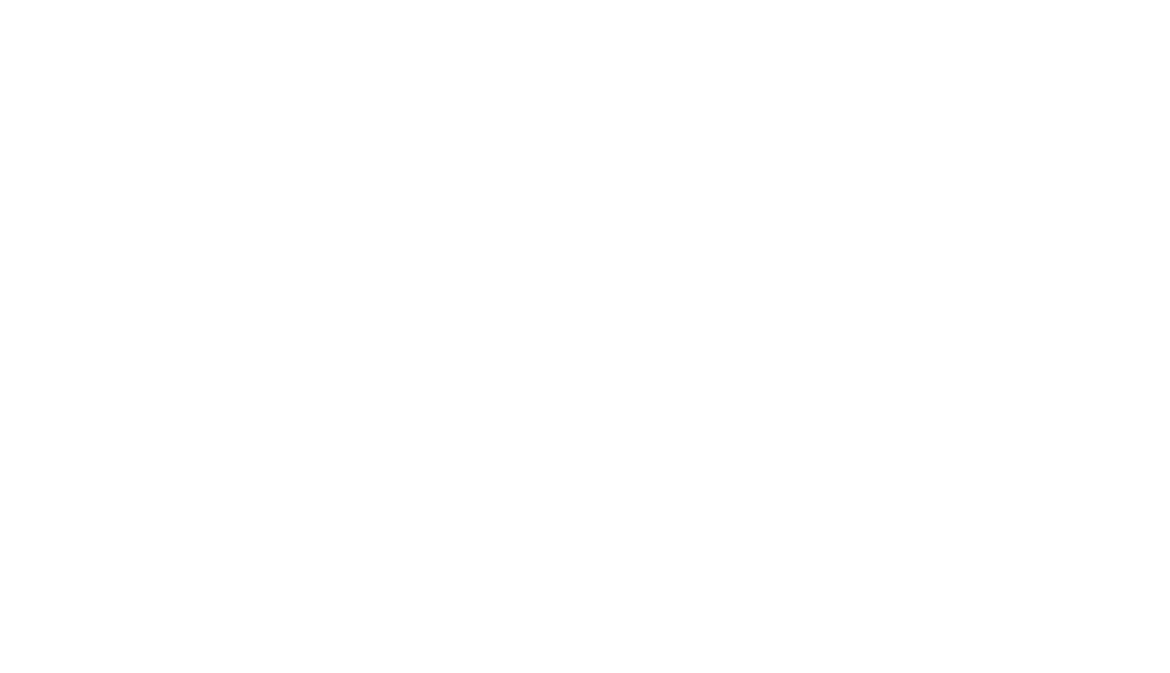
What's inside a wind turbine?
An overview of the layout of utility-class wind turbine generators. Where are the major components? What do they do? And what differences can be found between models and size ranges?
Video source: UVSAR / YouTube.
View TranscriptarrowWelcome. In this video, we’ll show you the layout of a typical wind turbine generator, as found on wind farms across the world. Now, exact designs do vary, but almost all the turbines in use today are horizontal axis machines which have a three-bladed rotor spinning in a vertical plane attached to the front of a box which we call the nacelle, after the fairing around an aircraft engine, and in this nacelle we have the generator, often a gearbox, and occasionally a high-voltage transformer, and the whole thing sits on top of a tower, which is mostly there to keep the blades from digging a hole. We tend to class turbines by their power output, and hence their physical size. Wind farms might use many sub-megawatt turbines, each producing 400–600 kilowatts each, or a few multi-megawatt turbines, producing maybe up to 3 megawatts per unit. Apart from physical scale, they are arranged a bit differently, so let’s start by looking at a typical sub-megawatt model.
Turbines of this type are typically 25 to 45 metres tall, and at the base you’ll often find two doors. The lower door takes you into a secured compartment where we have a high-voltage step-up transformer. The generator at the top of the turbine is producing about 690 volts, and this transformer converts that into several thousand volts to send it more efficiently to the substation. The main entrance to the turbine is at the first floor level, and there we find the control cabinet and the base of a ladder, or a series of ladders. Often in these smaller turbines, the ladders run to a series of platforms and they change sides at each platform to give you a rest area and a bit of fall protection. Platforms are generally just wooden discs suspended inside the tower walls, and they might have a trapdoor or a set of guardrails, and a gate, depending on how the landers are arranged. The main run of cables goes up the wall of the tower, and dodging past any intermediate junctions, because obviously the towers can’t be delivered in single 40-metre-long sections. They come in 20-metre-long sections that are bolted together with a lot of nuts and bolts.
As we move higher and higher through the platforms they’re getting slowly narrower and narrower, so the ladders are getting a little bit closer together, but eventually the main cables stop being attached to the wall and they hang freely in the centre of the tower so they can twist as the nacelle rotates to face the wind. If they twist too many times, the nacelle will spin itself around to remove the twists. But as we move up, now the cable goes through a hole in the centre of each platform, and at the top of the tower we have a steel platform with a steel trapdoor which we call the yaw platform. Just above that we have the yaw ring with the bearings which allow the nacelle and the rotors to rotate around to face the wind, and this steel platform acts as a bit of fire protection, also avoids people falling back down the tower, because at the top of the nacelle we simply have a hole, which we climb. And the nacelle in this case is a vaguely tapered tube. At the back we have the wind sensors which give us speed and direction, and allow the turbine to face into the wind and to change the angle of the blades. The nacelle itself is just a fibreglass tube. At the front we have a similar fibreglass cowl protecting the hub, which is a steel casting, on which we have bolted all three blades. And the blades can turn, or pitch, so that the angle they form with the wind can be varied. Out of the back of the hub we have a shaft which leads into the gearbox, and a high-speed shaft, through a break, into a generator. And that generator then supplies the electrical power, as I said, at around 690 volts, all the way back down the tower to the base. And right at the back we have a cooling fan. As we’re generating half a million watts of energy inside the nacelle some of that is wasted as heat, and without an efficient cooling system there is the potential for the turbine to catch fire.
Now the layout of a larger turbine is broadly similar. But some of the components are in different places. So let’s start by looking at the tower section of a typical 2-megawatt turbine.
Where we place the high-voltage transformers in multi-megawatt turbines is a lot more variable. Quite frankly, we have a lot more room, so we can decide. They can be in the nacelle, they can be at the base of the tower, they can be on platform one, in the basement, they can be outside in a hut. In this example, the transformer’s at the top, so when we go into our door, the one thing we will not find is a transformer. We do have the high-voltage switches, in this case on platform two, but on the entrance platform we have the usual control cabinet and a lift, a little green box. And that lift will take two people to the top of the tower, or nearly to the top, without them having to climb the single, very, very, long ladder. Almost all large turbines will just have a single run of ladder for the majority of the run of the tower, it will have a wire or rail system fall or rest device fitted to it, but it is still a long slog of a ladder, which is one of the reasons why service lifts are so important. And again, the tower’s in sections, so it can be delivered around the country without demolishing villages. Sometimes if we’re running a long distance and we haven’t got room for a proper platform, we can put a half-moon in place. No fall protection on the platform, but you’d assume you’d keep your lanyards connected at this point, because it’s quite a long way down. The cable, again, breaks free from its mounting and lays in the centre of the tower for the last 10–20 metres or so, so it can rotate as the nacelle yaws in the wind. And the lift eventually runs out of space. Remember, the tower is getting narrower and narrower as we get to the top, so the lift tends to park itself about half a platform from the top, and we have a normal ladder which then leads to the yaw platform, and then it starts looking very much like the smaller turbine did. We have a yaw ring bolted to the underside of the nacelle, joining it to the top of the tower, a series of disc breaks run around that yaw ring to lock it in position when the wind isn’t changing direction, and when it is, we have a series of either electric or hydraulic motors that rotate the entire mechanism around on the top of the tower.
The layout of a multi-megawatt nacelle is, again, more variable than for a smaller version. We always have to have a generator, but we may not have to have a transformer. In a few cases, such as in the famous Enercon egg-shaped nacelle we don’t even need a gearbox. They’re direct drive. You just have a shaft linking to a motor and then lots of extremely complicated electronics to condition that power for connection to the grid. But in most cases we need the same as we needed in the small turbine: a gearbox, generator, possibly a transformer, all in a fibreglass box. And in our example, we’re looking at a typical design used by a number of manufacturers where we have a nacelle that’s 3 metres high, 2 and a half metres wide, 7 or 8 metres long. It’s a fibreglass box that’s about the size of a site hut. As before, we have our wind sensors on the roof, as far away as possible from the dirty air cast off by the blades as they spin round. This design is just a fibreglass box with a flat roof. We access the roof through a couple of skylights. Some designs are, like before, big, cylinder, with two opening doors, some have an entire roof section that opens (rather like an old campervan). If we take the skin off the box, inside we have the same kind of components we had before. They’re just bigger, and there’s a little bit more room, so they’re laid out a bit differently. The only additional component, or pier, is those three green cylinders at the back. That’s our high-voltage transformer which used to be at the base of the tower. Now we’ve removed a lot of the control systems and the hydraulic systems that would just clutter in the pretty picture, we’ve added in a bloke for scale, but most of the big components are still here. If we look at the very front of the nacelle, we have a couple of bearings which support the main shaft, which is a hollow tube, 50, 60, 70 centimetres in diameter. It’s hollow so that we can get electrical cables in through the main shaft into the hub to drive all the control systems inside the hub, and we have a couple of pins on the first bearing that lock the main rotor in position if we need to access the hub. It’s a safety feature. If you’re in there and it starts rotating, it gets scary. So our main shaft drives our gearbox, which is mounted centrally because it’s often the heaviest component. Out of the back comes a high-speed shaft, as before, that’s where the braking system is. The high-speed shaft drives the generator, which is usually oil filled, the generator then supplies 690 volts in this case into our transformer which is sitting right next to it. That high voltage signal then passes through the switch gear in the cabinets, down the dropper cable, straight down to the bottom of the tower, through those switches on platform two, and off to the substation.
And that, as an overview, is pretty much all there is to it. The only thing left to talk about are the blades, obviously, which actually do the work. We still have three of them, they still pitch, in other words they twist on themselves to line up with the wind, and you access the hub through the gap between this fibreglass cowl and the cast hub. It’s a bit of a wriggle, but you wriggle through, usually feet-first, crawl through the hole in the middle of the hub, and inside the hub we’ll find the control electronics, the pumps, the motors, and the batteries, to control the pitch of each blade, rotating it on its own bearing to set the optimum angle for the wind. If we turn the blades through 90 degrees so they’re edge-on to the wind, there’s no net turning force, it’s a process called feathering, and the turbine will stop. Obviously there is a vast amount more going on inside a turbine, lots of wiring and control systems and lights and sensors and fire extinguishers etc., but that is basically it. The general overview of most turbines that you find on wind farms today.
Designs for the future will be significantly different, but at the moment, it’s a windmill on a stick.