The future of plastics
Expert reviewers
Essentials
- Since the 1950s plastic has revolutionised the way we live and become an essential part of our daily lives.
- The production and disposal of conventional plastics causes major environmental problems.
- Plastic pollution ends up in our streams, oceans, air and open spaces, resulting in the deaths of millions of animals annually.
- Scientists are working on a new generation of plastics known as ‘bioplastics’, products which can be tailored to be biodegradable or recyclable, and produced either fully or in part from renewable resources.
- Bioplastics are only part of the solution to the plastic problem—a change in consumer behaviour is also needed.
Why do we need bioplastics?
From the tiny buttons on your shirt, to the pen in your hand, from the keyboard you type on to the wrapping you remove from your sandwich, the intensive and extensive use of plastic in our society is undeniable. It has revolutionised the way we live and is an essential part of our daily lives. The figures speak for themselves—in 1960 the world produced 7 million tonnes of plastic. It’s predicted to rise to 540 million tonnes by 2020. But this wonder-product, which has transformed our lives in so many positive ways, has some serious environmental flaws in both its production and disposal.
Conventional plastics are manufactured using petroleum, coal or gas—all non-renewal resources susceptible to a volatile market of rising cost and demand, coupled with dwindling reserves.
However it is the disposal of these products that is of even greater concern. The irony is obvious—products that are intended to be used only once (such as food packaging and plastic bags), or to have limited or short-term use before being discarded, are manufactured in such a way that they will last a hundred lifetimes. This means that every piece of plastic you have ever looked at, used, opened or thrown away still remains somewhere in the world today.
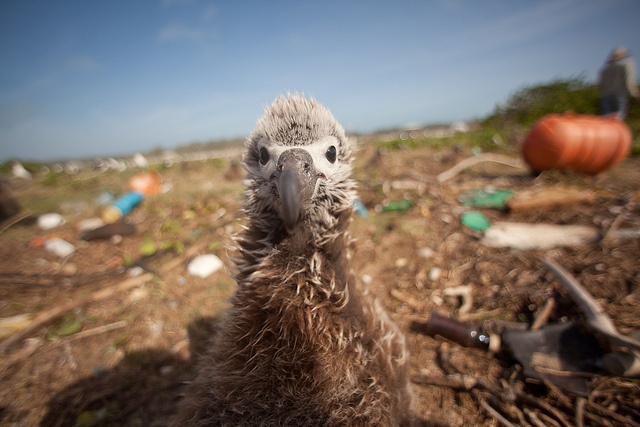
While some plastics are lucky enough to be recycled, most are sent to landfill, and the rest is left to its own devices, free to roam our environment clogging up streams, rivers, lakes and oceans, polluting forests and soils. There is even a new term for it: ‘white pollution’.
If you think it all sounds a bit depressing, you’re right, it is. But as plastic is too useful and too ingrained in our lives to be given up, scientists have been working on a new generation of plastics that can meet the needs of manufacturers and the community, while also providing benefits to the environment. Known as ‘bioplastics’, these products not only have the potential to be biodegradable and/or recyclable, but fully sustainable across all areas of their life cycle.
What are bioplastics?
The term bioplastic does not refer solely to biodegradable or compostable plastics made from natural materials. The name is also applied to petroleum-based plastics that are degradable, plant-based plastics that are not necessarily biodegradable, and plastics that contain both petroleum-based and plant-based materials that may biodegrade or not.
Essentially, bioplastics are bio-based, biodegradable, or both.
The term ‘bio-based’ means that the material or product is at least partly derived from biomass (plants). Examples of biomass used in bioplastics include corn, sugarcane, tapioca, or other forms of cellulose.
Biodegradable generally refers to a substance that can be broken down by microorganisms in the environment within a fixed period of time. Effective biodegradation requires specific environmental conditions including temperature and level of aeration, allowing microorganisms to convert natural materials into other natural substances such as compost, water and carbon dioxide.
With bioplastics, biodegradability is directly linked to the chemical structure and not necessarily to the origin of the raw materials.
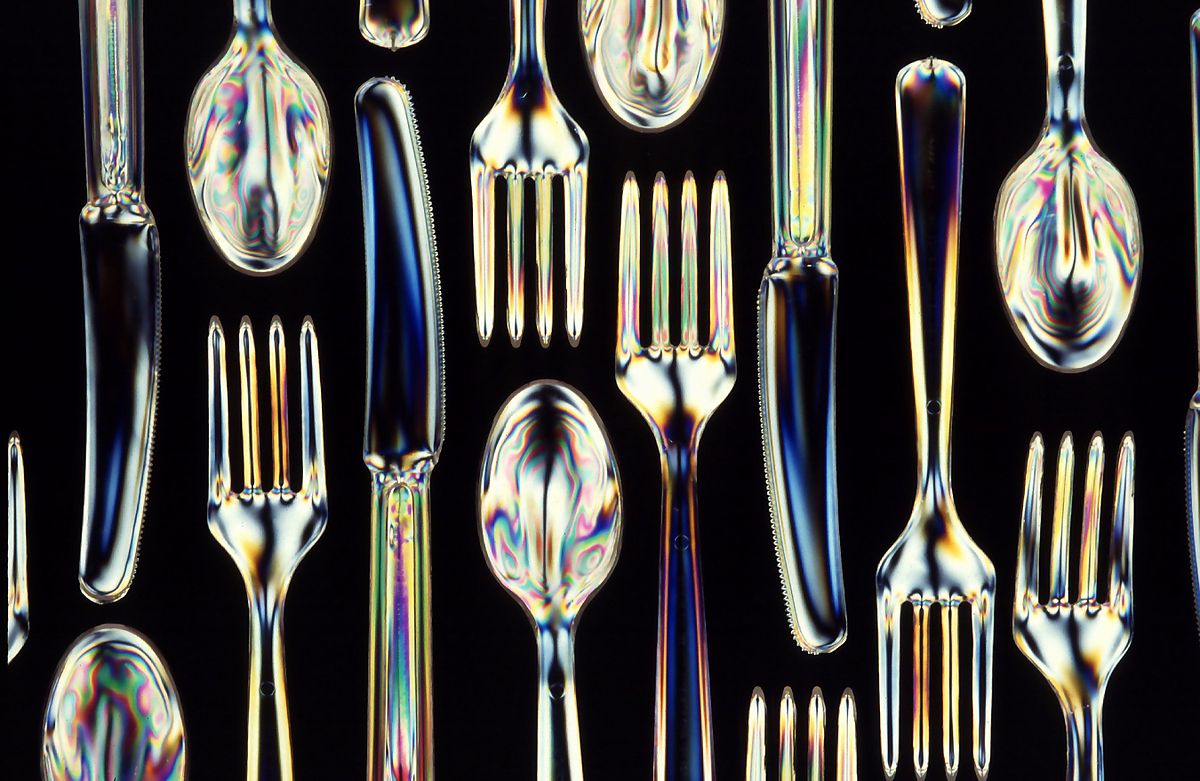
Plastic cutlery made from a biodegradable material. Image source: Agricultural Research Service via Wikimedia Commons.
Types of bioplastics
Bioplastics are not one single substance—rather, they are a family of products each with differing properties and applications depending on their base materials and manufacture.
Currently, the bioplastic family can be divided into three main groups:
- Group 1: Plastics that are both bio-based and biodegradable
- Group 2: Bio-based or partly bio-based non-biodegradable plastics, known as ‘drop-ins’
- Group 3: Plastics that are based on fossil fuel resources and are biodegradable
Group 1: Plastics that are both bio-based and biodegradable
Examples: polylactic acid (PLA) and polyhydroxalkanoate (PHA)
Group 1 bioplastics consist of products that are both bio-based and biodegradable. They can be made from a number of different natural sources including plants, cellulose, protein, chitin (prawn shells) and bacteria.
Derived from the starch of natural and renewable resources such as corn, wheat or potatoes, polylactic acid, also known as polylactide and commonly referred to as PLA, is currently one of the most popular and promising ‘green’ plastic alternatives on the market.
The creation of PLA involves several steps. First, corn undergoes wet milling, a mechanical process that separates the starch, along with other useful components, from the kernel. The starch is then heated with enzymes or acid (or both), to completely hydrolyse GLOSSARY hydrolyseaThe break down (a compound) by chemical reaction with water the starch to dextrose. The resulting dextrose can be in either crystalline or liquid form.
Through a process of fermentation GLOSSARY fermentationThe chemical breakdown of a substance by bacteria, yeasts, or other micro organisms. , the dextrose is converted to lactic acid, a relatively simple organic chemical compound. This is the same kind of lactic acid that torments your muscles after vigorous exercise, but produced on an industrial scale. The lactic acid then undergoes polymerisation GLOSSARY polymerisationAny process in which relatively small molecules, called monomers, combine chemically to produce a very large chain-like or network molecule, called a polymer. to cause the molecules to link up into long chains or polymers which bond together to form PLA. This is turned into sheets of flat plastic or pellets, which can then be moulded into a variety of different forms including containers, films and fibres.
The characteristics of PLA are similar to those of conventional petrochemical plastics (such as PET), while another benefit its ability to be processed on existing plastic production equipment.
Alongside its renewable base materials, one of PLA’s strong environmental selling points is its ability to completely biodegrade. Because it is made from plant-based sources, it makes a ready meal for bacteria and other microbes to feast on. However, due to its production process, if placed in your backyard compost bin or sent to landfill, it will behave just as any regular petro-plastic—that is, it will take many decades to disappear. To fulfil its biodegradable potential, PLA requires specific compost conditions. Unfortunately, these can only be found in industrial composting facilities, of which there are relatively few.
PLA’s increasing popularity has seen its uses expand from primarily food packaging to encompass a wide range of fields including medical, textile, automotive, cosmetic and household applications.
Another ‘Group 1’ bioplastic is polyhydroxalkanoate, or PHA. PHAs are naturally occurring polymers that can be produced in different ways by specific strains of bacteria. In the first instance, bacteria is exposed to a limited supply of essential nutrients such as oxygen and nitrogen, which promotes the growth of PHA—granules of plastic—inside its cells as food and energy reserves.
A separate group of bacteria has also been identified that do not require nutrient limitation for PHA production, but accumulate it during periods of rapid growth. The PHA within both these groups can then be harvested, or, prior to harvesting, can be synthesised into different chemical forms via genetic engineering.
Initially, the commercialisation of PHA was hindered by high production costs, low yields and limited availability, making it unable to compete with its petrochemical counterparts. However, recent breakthroughs have found certain bacteria that are capable of producing PHA from a range of carbon sources including waste effluents, plant oils, fatty acids, alkane, and simple carbohydrates. This greatly broadens their appeal—for example, using waste materials as a carbon source for PHA production would have the dual benefit of reducing PHA cost and reducing the cost of waste disposal.
In 2013 an American company announced that it had refined the process even further, removing the need for plant-based sugars, oils, starches or cellulose, instead using a ‘biocatalyst’ derived from microorganisms which converts air mixed with greenhouse gases such as methane or carbon dioxide directly into plastic.
Taking this stream of PHA research even further, scientists are taking the genes from this plastic-growing bacteria and inserting them into corn plants, which then grow the plastic in their own cells. Farmers producing these genetically modified corn plants effectively ‘grow’ a crop of plastic.
PHA is fully biodegradable under the right conditions, non-toxic, and can be used in a wide range of applications, from food packaging to medical implants.
Group 2: Bio-based or partially bio-based non-biodegradable plastics—‘Drop-ins’
Examples: bio-polyethylene (PE), bio-polypropylene (PP) and bio-polyethylene terephalate (PET)
Drop-ins are bioplastics that are bio-based or partly bio-based, but are not biodegradable. Put simply, ‘drop-in’ solutions are hybrid versions of traditional plastics. They differ from their conventional counterparts only in terms of their partly renewable raw material base, while retaining the same functionality.
Leading the field is partially bio-based PET, which is already accounting for approximately 40 per cent of the global bioplastics production capacity.
Many conventional plastic types such as polyethylene (PE), polypropylene (PP) and polyvinyl chloride (PVC) can in fact be made from renewable resources, such as bioethanol.
A popular example of a drop-in plastic is the ‘Plant Bottle’ currently used by one of the world’s leading soft-drink manufacturers. The bottle uses 30 per cent plant-based materials in its manufacture, while retaining the same characteristics as the traditional bottle, and also being fully recyclable. Over time, it is hoped that the renewable component of the bottle will increase, while the fossil fuel-based materials will decrease.
Drop-ins are the fastest growing bioplastic group. Industry interest is based around two main selling points:
- Drop-ins feature the same properties and functionality as their petrochemical counterparts, meaning they can be processed, used and recycled in existing facilities and following the same routes as conventional plastics. This reduces the need for new or additional infrastructure and reduces costs across all levels.
- The renewable (or partly renewable) basis of these products reduces their carbon footprint while also lowering production costs.
Group 3: Fossil fuel-based plastics that are biodegradable
Examples: polybutyrate (PBAT) and polycaprolactone (PCL)
The last group of bioplastics are new polymers that are based on fossil fuels but are still biodegradable, and include products such as polybutyrate adipate terephthalate—known more commonly as polybutyrate or PBAT. Used primarily in conjunction with starch or other bioplastic materials, they improve the application-specific performance of the final product due to their biodegradability and mechanical properties. Though currently still produced as hybrids with petrochemical plastics, new bio-based or partly bio-based versions are in development.
PBAT is a random copolymer GLOSSARY copolymerA random copolymer is a polymer comprised of two or more different mer units (a group of atoms that constit a polymer chain repeating unit) attached in a random order. made up of butylene adipate and terephthalate. It is fully biodegradable under correct composting conditions, and contains many properties which are similar to low-density polyethylene such as high elasticity, fracture resilience and flexibility. This makes it a viable alternative for use in products such as bags, wraps and other packaging. It is particularly suited to rubbish bags or disposable packaging due to its ability to decompose in compost within several weeks. PBAT can also be used as an additive, giving rigid bioplastics more flexibility while retaining the biodegradable properties of the final product.
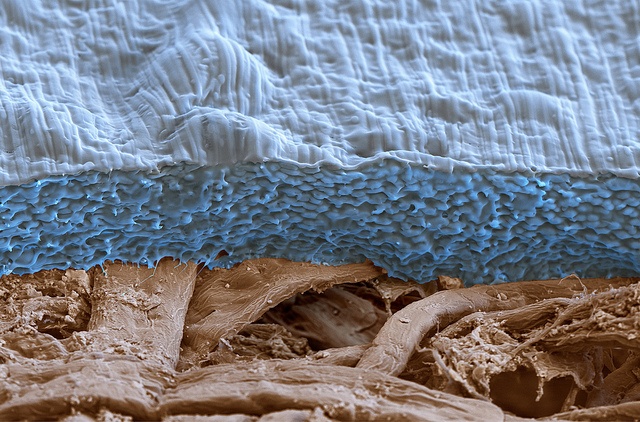
Paper packaging is sometimes covered in polyethylene, which causes a problem for recycling. This is an electron microscope image of a biodegradable alternative. Image source: BASF on Flickr.
Environmental pros and cons of bioplastics
There are two sides to every story, and bioplastics are no different. They have great potential and many positive attributes, yet these are countered by an almost equal number of drawbacks. Both sides of the equation need to be considered closely when considering the environmental impact of bioplastics in our society.
Pros
- They reduce the use of fossil-fuels and reliance on non-renewable resources.
- Manufacturing process can use up to 65 per cent less energy and generates fewer greenhouse gases than conventional plastic.
- Some are biodegradable and/or compostable.
- Some can be recycled alongside conventional plastics.
- Some are non-toxic and safe for medical and internal use.
Cons
- They have a higher manufacturing cost—though this is changing as more companies begin to make bioplastics.
- Composting may be possible only in industrial composting processes.
- Not all are recyclable.
- Some can interfere with or damage standard plastic recycling processes.
- Not all are biodegradable.
- If sent to landfill, some can release methane—a potent greenhouse gas—into the atmosphere.
- They’re not suitable for use in a number of products.
- Use of plant sugar and starch sources could have a negative impact on food prices.
- Bioplastics do nothing to change consumer behaviour regarding their use of plastic products.
Market demand
Demand for bioplastics is growing. Advances in technology have improved product quality and versatility, while lowering production costs. This, in conjunction with rising fossil-fuel costs, has resulted in more companies entering the bioplastic market, promoting further research and competition. The renewability and availability of raw materials, the various disposal options for bioplastics, coupled with rising consumer demand for environmentally responsible products has led some to claim the industry has hit its ‘ tipping point GLOSSARY tipping pointThe point at which a series of small changes or incidents becomes significant enough to cause a larger, more important change. ’.
At present, bioplastics make up around 1 per cent of the total plastics market, a tiny drop in the plastic ocean. However, analysts forecast strong growth within the sector. Published market reviews on bioplastics project growth rates ranging from 15 to 35 per cent between 2010 and 2020. By 2018 production capacity of bioplastics will be over 6.7 million tonnes. The top performers are expected to be the drop-ins such as bio-PET and bio-PE, followed by PLA. This reflects the industry’s move away from fully compostable products to those that already have established recycling streams. While PLA is compostable, the low number of industrial composting facilities are currently reducing its appeal.
A 2010 study estimated that the technical substitution potential of bioplastics for replacing conventional plastics could be as high as 90 per cent. This means that bioplastics have the potential to eventually replace most of the conventional plastics that are currently used in everyday life. As the growing commercialisation of bioplastics continues to result in lowered costs and improved technological capacities, the reality of such a figure may begin to seem more attainable—though still a long way off.
We must all begin to live in a smarter materials world. [Bioplastic] innovation isn’t the total solution to the problem of plastic waste, but it’s a critical start.Brendan Morris, CEO of Plantic
What else can we do?
Bioplastics are a great innovation, but they are not the only solution to the problem of plastic pollution in our environment. A change in consumer behaviour—in the way we think about, use and dispose of plastics—is essential in effecting longer-term change.
Below are just a few simple tips to help you cut down plastic use in your life.
Be proactive
Take the time to educate yourself about the full ‘cost’ of plastics, and inform family and friends of ways that they too can cut down their waste. Try and implement the four ‘R’s—Refuse, Reduce, Reuse, Recycle. Every little bit helps.
Say no to plastic bags
Over one trillion plastic bags are used worldwide every year—bring your own reusable bag or just say ‘no thanks’ at the check-out.
Bring your own bottle
Bring your own refillable drink bottle and/or coffee cup instead of buying disposable, single-use plastic bottles.
Opt for less packaging
Have you ever bought a product and had to unwrap multiple layers of plastic before being able to use it? Try to buy products that have less plastic packaging, or, better yet, opt for ones that come in cardboard or other recyclable materials. Support companies who are trying to reduce their packaging to a minimum.
Pack a ‘green’ lunch
Instead of wrapping your sandwich and snacks in plastic wrap, pack them in reusable containers.
Buy refillable products
Where possible, buy products (such as lighters, pens and so on) that can be refilled rather than those that are single use.
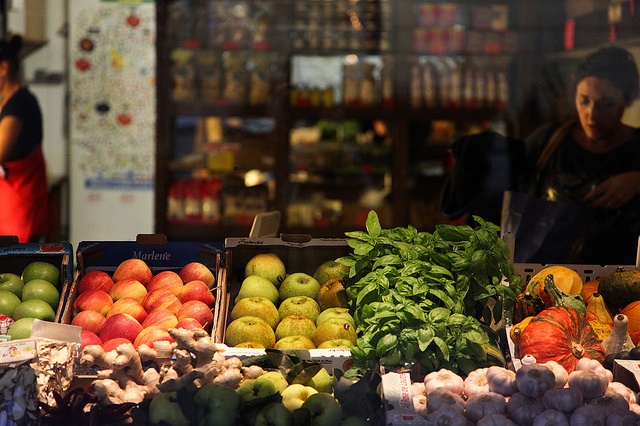
The choices you make at the shops and at home can help reduce plastic pollution in our environment. Image credit: ornello_pics on Flickr.
Conclusion
The idea of bioplastics is of considerable interest and importance in the modern world. To develop a product that not only meets the needs of manufacturers and consumers, but which actively reduces environmental pollution, is a key goal of researchers and scientists in this industry. The current generation of bioplastics, while far from perfect, has some remarkable traits, and continuing research into this field will enable further breakthroughs and improvements. However, bioplastics are not the only solution. Consumers need to recognise that the many positives plastic brings to our lives are balanced out by an equal number of negatives. Changes in the way we buy, consume and dispose of plastics are just as important as any scientific breakthrough.